The Journey of Your Online Purchase
Let’s follow the path of a theoretical $20 T-shirt you’ve bought online. The journey begins in the overseas factory it was likely produced in and ends at your home. The shirt is manufactured at a factory in Vietnam, packed, and loaded onto a container which is placed on a truck, and from the truck onto a river barge which delivers it to a port. From the port, the container it’s in is loaded onto an ocean freight liner and makes a 2-3 week trip to the shores of the USA.
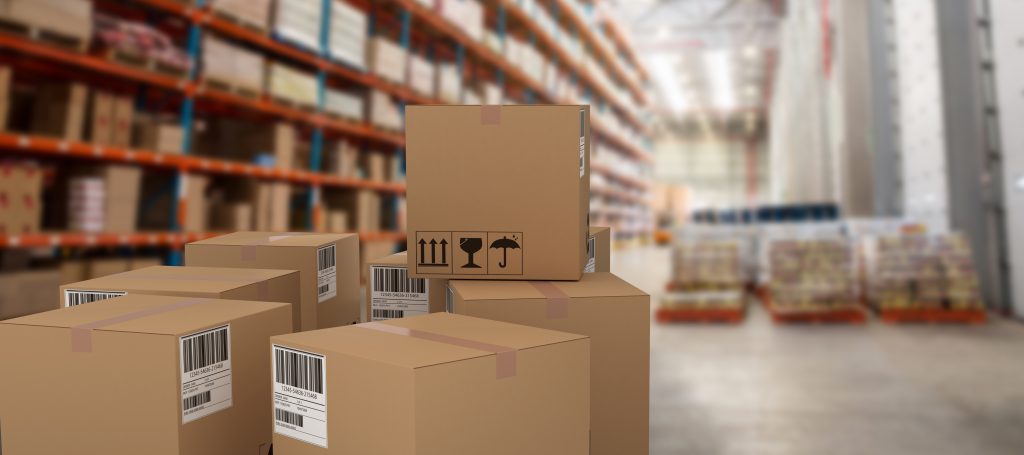
At the port of entry, the container is unloaded onto the dock, sorted, and stacked to await pickup by a truck that takes it to a local fulfillment or distribution center. At the distribution center, it is unloaded. The products (your T-shirt) are sorted, counted, inspected, and stored until it is ordered. At that point, it will be loaded onto yet another container where it will make its way by long haul truck to a distribution center closer to where you live. Again it will be counted, inspected, and stored. When you order it, it will be picked and packed and make its way to the Last Mile delivery vehicle.
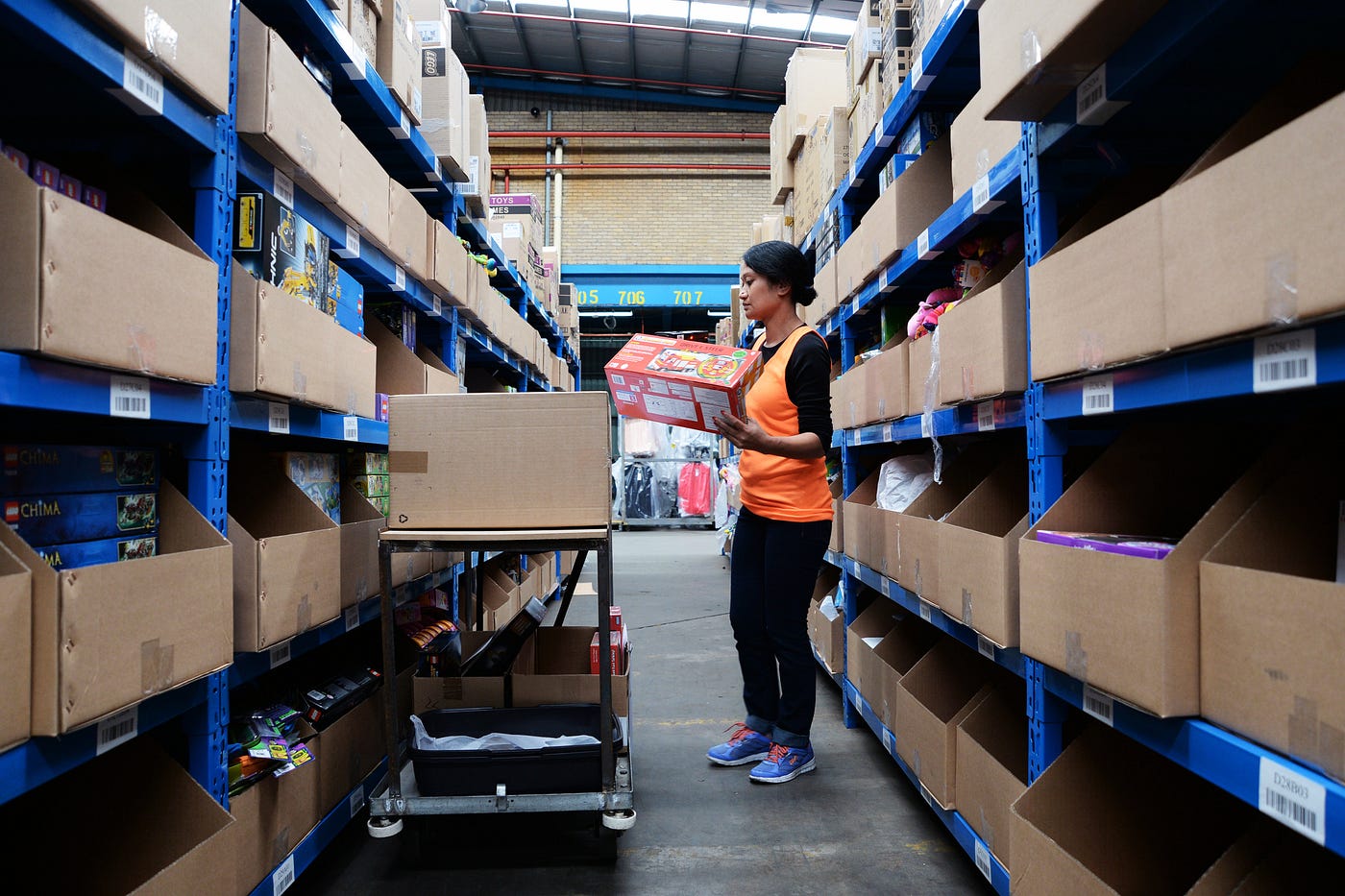
You placed the order for the T-shirt yesterday and received it today, but the journey the shirt took to get to your home most likely lasted two months. You probably encountered no human being in the transaction, save the Last Mile driver, and that is only if you were home at the time of delivery. Your T-shirt, however, has been handled by multiple people; factory workers, inspectors, haulers, truckers, sailors, merchant marines, longshoremen, warehouse workers, and more truckers. All in all, our figurative $20 T-shirt has been “handled” by as many as 100 people, perhaps more.
Not too long ago, we didn’t pay much attention to this process at all. After all, these systems were built for our convenience and are made to be as affordable as possible. Covid and the lockdowns that came with it put a spotlight on the vulnerabilities of this process which is known as the supply chain (logistics) and the costs associated with it. Before Covid, any single disruption to the supply chain caused minimal to no disruption in the process or the price, because of the vastness and complexity of the overall logistics ecosystem which had organic fixes built into it. Covid basically caused a power outage in the supply chain with subsequent rolling blackouts that we are still trying to repair.

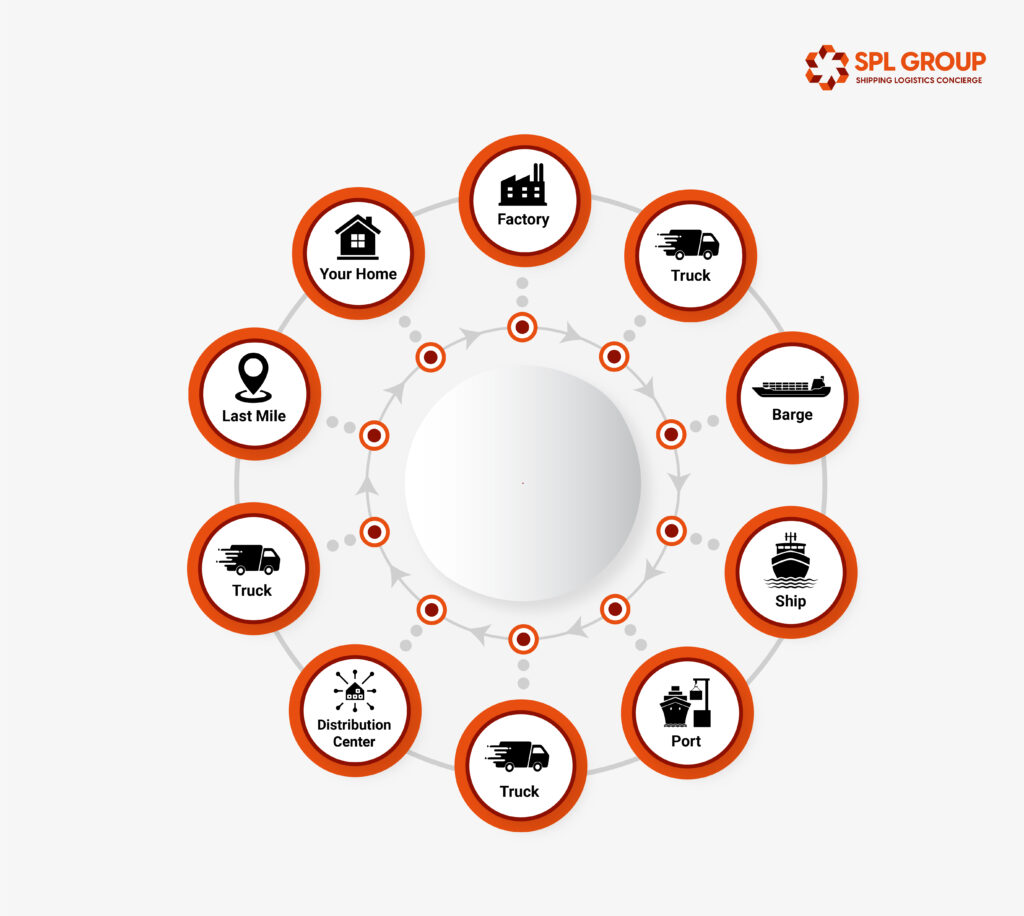
Disruptions
As the above flow chart illustrates, the process is vulnerable to disruptions, possibly multiple disruptions. As a consumer, you may feel the disruption by either not receiving your T-shirt or getting it later than you expected. So, if there was a fire in a factory in Vietnam, one or two containers got lost in a crowded port, a truck crashes, a ship disappears in the Bermuda Triangle, or any other scenario we can create – occurs, this will affect hundreds perhaps thousands of buyers. Consumers can turn to other sellers or wait to buy the T-shirt sometime in the future, but the global supply chain continues.
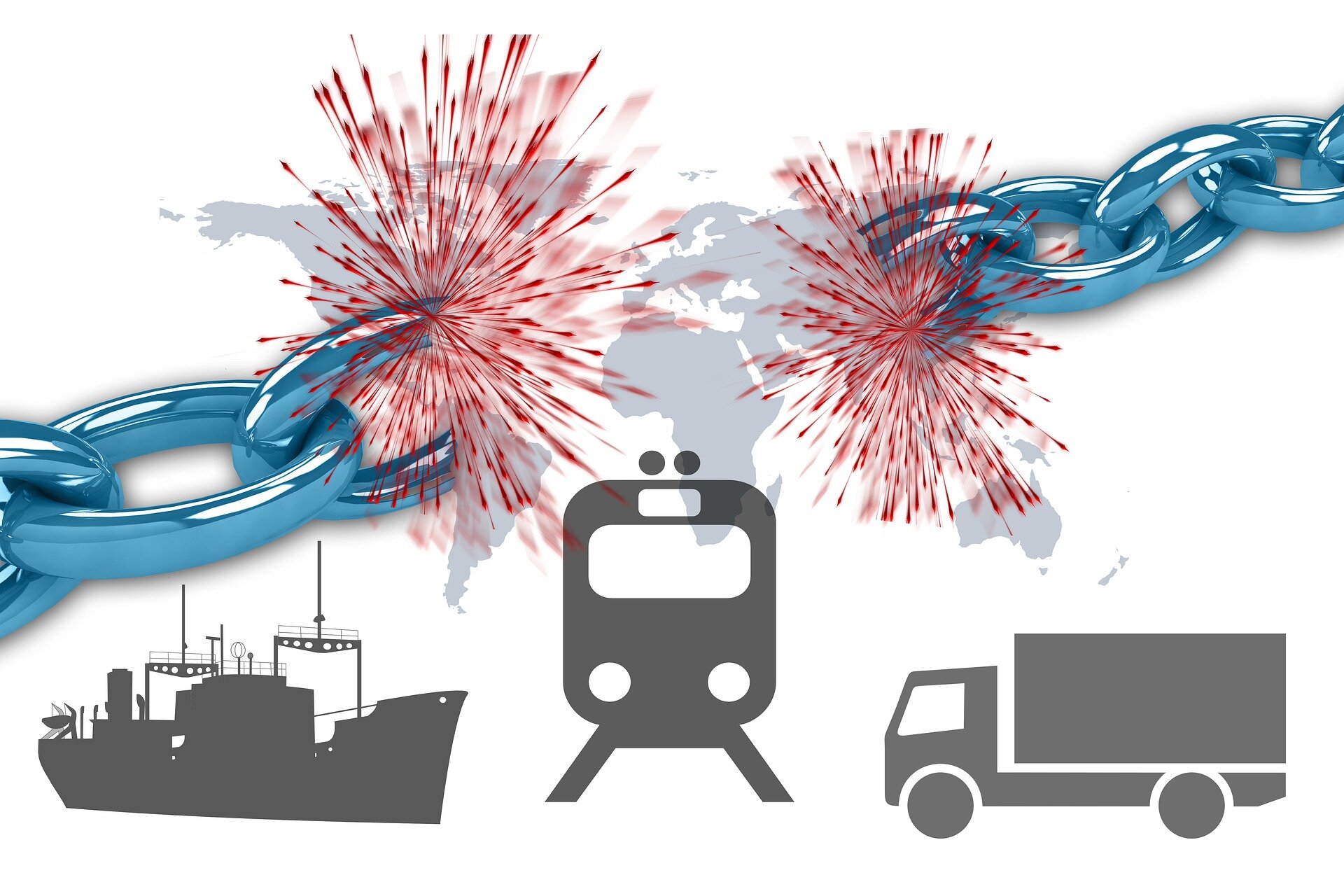
The above examples of delivery glitches don’t really speak to the resilience of the supply chain in the pre-Covid world. Pre Covid, the worldwide supply chain was able to withstand severe weather episodes, labor strikes, material shortages, and other large scale events. A strike by dockworkers on the West Coast might have detoured sea freight traffic to the East Coast for a time. A Tsunami in Asia might have forced retailers to accept low levels of inventory in their warehouses for a time etc….
Covid exposed one key weakness to the supply chain that has been developing for 40 years. That weakness, of course, is the failure of the global supply chain to withstand multiple large disruptions at once. Let’s be clear about one important fact, the supply chain failure did not occur solely in the vacuum that was Covid, it has been building over time with deregulation, technological innovation, purchasing habits, and consumer expectations. This became the inevitable perfect storm.
In our next post, we will explore how Covid interrupted every step of the supply chain from factory to Last Mile delivery.